What to Know About Wood Veneer Fabrication
One of the things that sets DTANK+ apart from other custom furniture companies is our comprehensive ability to work with a variety of different materials. From hot rolled steel to laminate to wood veneer fabrication, the possibilities for custom solutions are limitless. Even more importantly, our products are made from high-quality materials that are built to last.
Our team understands that selecting the best materials for your project is not always easy, especially when there are so many options at your fingertips. It can be particularly challenging to determine the best options when you are using wood veneer. Specification of this material requires careful consideration of the wood type, grain type, finish, and more. At DTANK+, we are happy to share our fabrication expertise with our clients and provide guidance throughout the material selection process. Keep reading to learn more about wood veneer, so that you know what to expect for your custom project.

Selecting a Species
The characteristics of wood species can vary greatly, so it’s important to keep this in mind during the material selection process. Our goal is to help you strike the right balance between aesthetics and durability.
Wood species are categorized as either softwood or hardwood. If you are going for a streamlined look, softwood has a softer grain with less knots and contrast. Hardwood is characterized by more variation and texture in the grain, giving it a warm and sometimes rustic appearance. It is thick, dense, and porous. The strength of hardwood makes it easier to cut than softwood. It is a great choice for furniture fabrication because it will last a long time and it has good resistance to the elements.
Below are some of the most common species used in wood veneer. Softwoods include cedar, fir, and pine. The rest of the species pictured are hardwood.
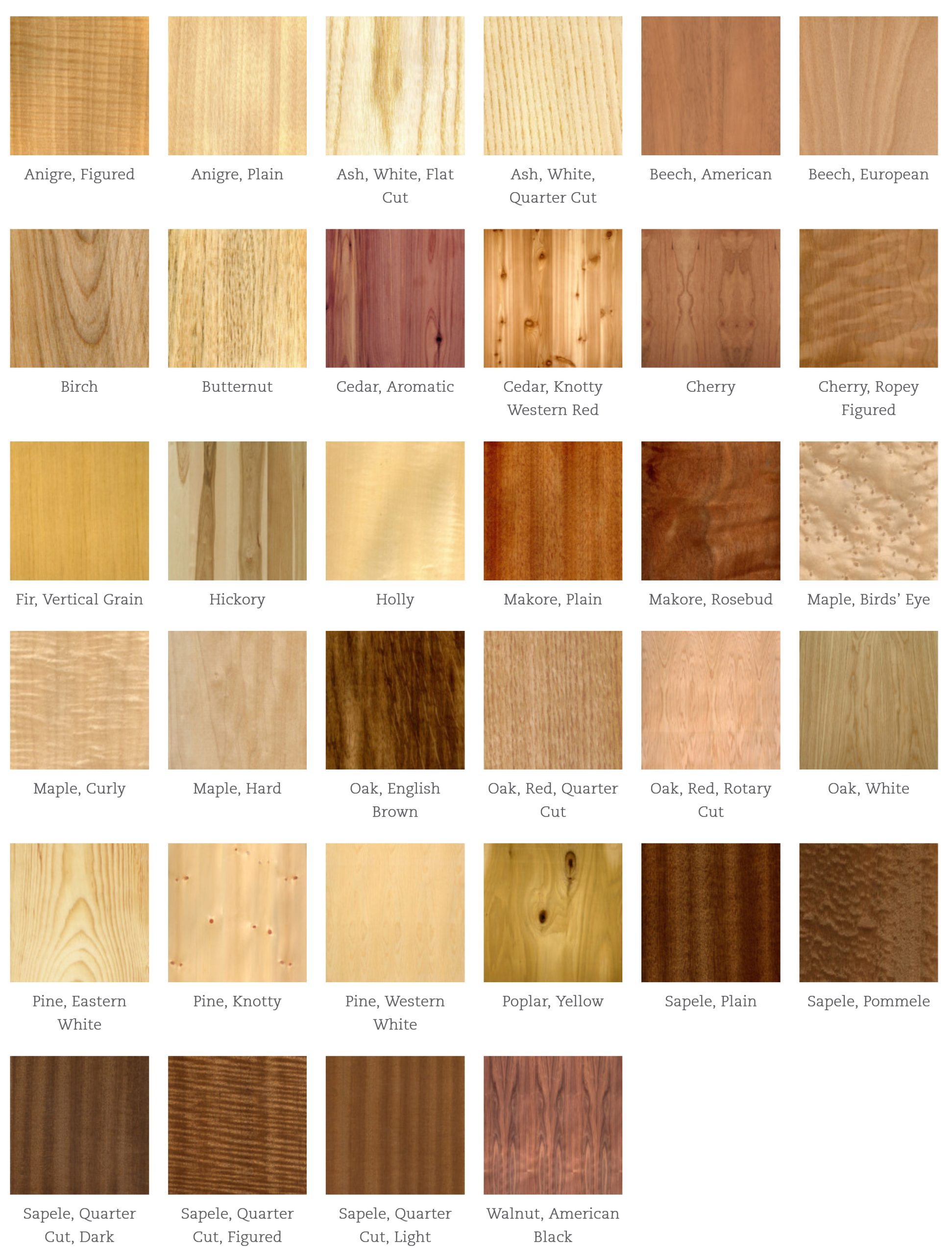
Choosing a Cut
Another factor that affects the look of wood veneer is the cut type. Veneer is essentially a thin sheet of wood that has been attached to a stronger substrate, like MDF or plywood. Depending on the type of wood that you select, there are many techniques for producing the top sheet. Each one creates a different pattern for the grain, altering the overall style of a furniture piece fabricated from wood veneer.
All species of wood can be plain sliced, quarter sliced, or rotary cut. Other cutting methods are possible only for certain types of wood, making them more expensive. For example, oak is typically used for rift cut veneer because it produces a very straight, uniform grain.
Here is a closer look at the most widely used cuts and how they are produced:
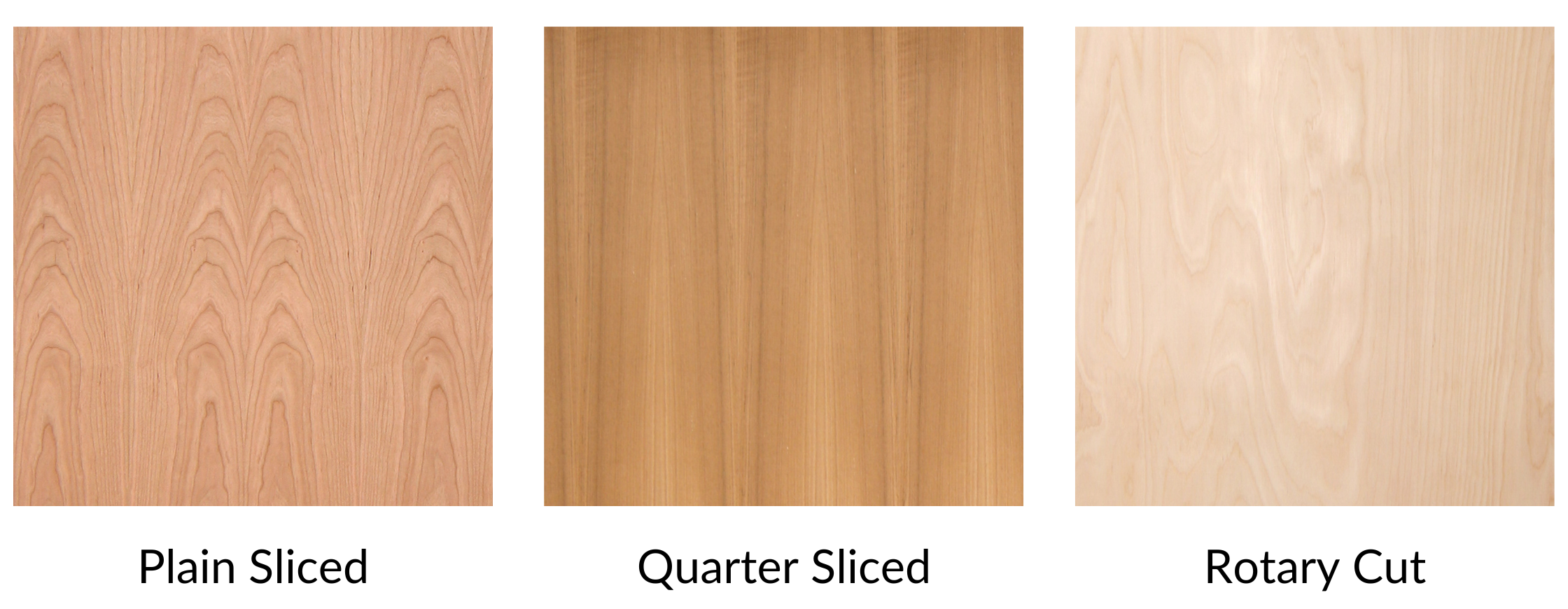
Plain Sliced
This type of cut is also referred to as “plain sawn” or “flat cut.” It is produced by sawing a log in half, then slicing the wood parallel to the round face. Plain sliced wood veneer is considered the standard for furniture. It has a pattern with a cathedral effect, or distinct arches that allow for a lot of color variation within one slice. It is also the most used cut for book matching veneer.
Quarter Sliced
This cut is produced just as it sounds. A log is cut into quarters, and then each quarter is sliced perpendicular to the round face. The result is a grain with thin stripes, which are often straight. Quarter slicing produces narrower sheets than plain sliced veneer, making it an excellent choice when you want to match the grain on a large piece. While all species of wood can be quarter sliced, it is especially popular for oak because of the unique flaked pattern it creates.
Rotary Cut
Rotary cut veneer is produced when an entire log is turned and shaved, following the circumference of the circular face. This is considered to be the most budget-friendly veneer cut, and it produces the smallest amount of waste. It works well for large pieces of furniture because the veneer can be one continuous sheet. However, there is less consistency in the grain, making the pattern less striking and often less desirable for furniture applications.
Finding the Right Finish
Once you have selected a wood species and cut, it’s important to find the right finish that will add a layer of protection to your custom piece. Finishes contribute to the overall look of a piece, but the appearance can change over time. They also play a major role in determining longevity. You’ll want to consider these factors carefully, in order to select the most appropriate finish for your piece.
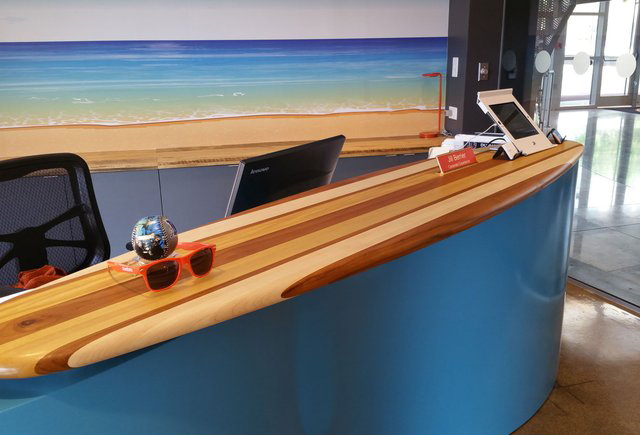
Common finishes include:
- Varnish: This is perhaps the most widely used finish on the market. It forms a plastic-like coating that is scratch-resistant. Varnish also soaks into the pores of hardwoods, enhancing the natural colors of it. It comes in a variety of different sheens, ranging from high-gloss to matte, to achieve your desired aesthetic. When properly treated, furniture with varnish can last for up to 20 years before it needs to be refinished. However, varnish can yellow over time. Heat and lack of sunlight can speed up the yellowing process.
- Polyurethane: Like varnish, this finish hardens with a plastic look to it and has a long lifespan. It is stronger than varnish and more resistant to the elements, but it also yellows more quickly.
- Lacquer: If you’re looking for an alternative that doesn’t yellow, lacquer is your best choice. The hard coating also provides the best protection against chips, scratches, and dents. Unlike varnish and polyurethane, though, it is only available in a high gloss sheen.
- Hardwax oil: This finish provides a thinner coating and less protection than the others, but that also means that it is easier to reapply. It does not alter the color of the wood, as some of the other finishes do. In fact, hardwax oil can actually improve color retention for wood veneer. This is a great choice for environmentally conscious individuals and companies because it is typically non-toxic.
In addition to these finishes, you can also choose from a wide range of wood stains to enhance the look of your custom piece. We can use stains to match your company’s branding, establish a signature style, and make an impact on everyone who visits your space.
Whether you decide on wood veneer fabrication or one of many other material options, our team at DTANK+ can guide you to the most practical solution for your project. All of our products are manufactured in the United States, which helps us ensure quality, reduce our carbon footprint, and keep costs down for our clients. You can rest assured knowing that our products are backed by a 10-year warranty, too.
When you’re ready to start selecting materials for your project, reach out to our team! We can help you visualize your concept with free renderings, share our extensive knowledge of materials, prepare engineering drawings for your design, and more. We are here to support you through the custom fabrication process from concept to completion!